While in a "burner making" frame of mind, it seemed like a
good idea to supplement the Oliver Upwind Burner
with something a little larger for melting cast iron.
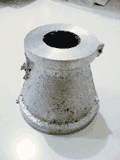 |
28-Aug-2002: The casting for the reducer. You can click
here to see more details on how it was made.
This casting is not going to win a beauty contest but it will do the
job. |
Update 30-Aug-2002: What a mess... I found out
that 1.1/4" pipe means bore size, not overall diameter.
This is not going to work out as a Monster Burner in a million
years. However, I can cut the burner tube down from 12" to
9-9.5" in length and the proportions should work out about
right. Saves throwing the new casting away. |
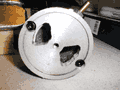 |
Update 31-Aug-2002: There are two castings on the end of the bell
housing, the first has some rough cutouts to allow the air intake to be
choked. The two end castings were made simply by pushing a tuna can
into green sand and just pouring ali straight in. |
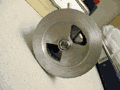 |
Another casting goes on the end of this with matching cutouts so that
the air intake can be reduced. The casting shown here rotates over
the casting shown above. |
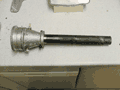 |
The final assembly... It works pretty well, the only problem is
that the small cutouts on the choke plates will only supply enough air for
about 18psi worth of gas before it gets too rich. |
Summary: Even with the restricted choke
opening, this burner will still scare the living daylights out of my small
furnace. If I can get some more air in, 30psi should be achievable
with the 1.00mm jet size. Update: The rich running may have been due to
me opening the choke up so much it started closing again :-( The
bell housing has now been painted light blue and marked with a sharpie
where the min and max are, so I can give it another run at the weekend and
try again.
Update #2, Sep 5th: Have run again with the markings on the
choke so I know where "max" is. It will now do the full
30psi from the regulator and runs quietly with a sweet roar.
Knocking the choke back to half, it will run down to very low gas levels
and is stable at low levels. Sometimes there is a "whoop
whoop" effect on low gas levels running rich as a flame ignites and
goes out in the exhaust port. Some pictures: |
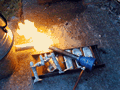 |
As described above, the bell housing has been painted light blue and
marked min/max. Just a tiny smidgen of gas with the choke fully shut is the normal
lighting up procedure. Once the burner is in, the gas can be turned
up to the required level (with the choke still shut), with a smoky flame
coming out of the top of the furnace. The air is increased, the roar
gets louder, and the flame drops inside the furnace. |
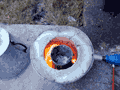 |
This is with the top off @ 30psi. Note that this is straight after
the burner has been fired up. When the furnace gets hot, the air has
to be choked a little or an oxidising flame results. I'm guessing
that this is due to the hot lining causing more of an up draught and
pulling more air in. |
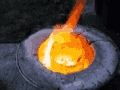 |
After just a few minutes it becomes apparent that there is plenty
of power available. The ali has not started to even think about
melting yet, but the steel crucible and lining have reached
temperature. At this point, I decided to reduce the power
substantially. This picture was taken shortly after the one above,
it just looks dark because of the amount of light coming from the crucible
and lining. |
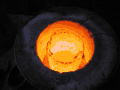 |
Finally, a pot with a couple of pounds of molten ali ready to be poured. |
This little burner is now melting iron, please check the cast iron
page for more details and a video of the burner in action. |