Home
Up
|
The Spindle
The spindle contains the shaft on which the grinding wheels are mounted.
Due to the use of angular contact bearings and a preloading mechanism, there should
be no radial or axial play in the spindle over a wide range of temperatures.
Chaddock based this design on one recommended by RHP with some minor changes.
401: Spindle body
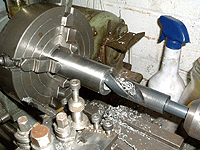 |
26-Dec-06: The spindle is being drilled from both ends to 9/16" initially, these will
then be bored out to the correct size. The stock is 1-3/8" in diameter and has been cleaned up and
centred very accurately. Further checks are carried out after drilling to see if the work has moved in
the chuck. |
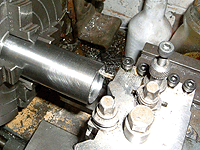 |
Quite a time consuming job - this is the last bit of threading which is almost the conclusion of 6 hours work to do all the drilling
and boring. Just the tapping
for the 2BA countersunk screw to carry out now. |
Trepanning tool
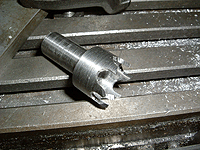 |
28-Dec-06: Here's the smaller of the two trepanning tools that are needed. This one will be used to cut the
circular slot in the pulley. A slightly larger trepanning tools is sitting in case hardening compound at 700 degrees C for
4 hours, a first attempt at case hardening. This one is next for the heat treatment... |
As a footnote, the 4 hours at 700C in case hardening compound was a waste of time - the part came out softer than the item it was trying to cut.
The second attempt saw 880C (1620F) for 3 hours followed by a straight quench which gave perfect results.
404: Endcaps
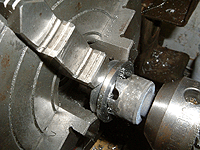 |
29-Dec-06: This is one of the last tasks on the endcaps, cutting the groove in the face. The hardened mild steel cutter
is working a lot better than I expected. |
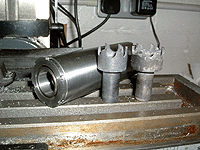 |
The final job is to mill 6 slots in each cap by mounting on a 0.690" arbor and mounting in the dividing head.
I couldn't resist this picture of the spindle, the two cutters look like King and Queen Quorn! |
410: Spindle shaft
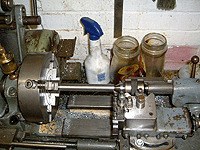 |
30-Dec-06: Between centres is probably a better way of dealing with this item, but the old Myford is well worn and
there's no guarantee of accuracy. Two short sections were machined to 0.5115" with a relief put between
them - it seemed easier to get a short section the same diameter along the length. |
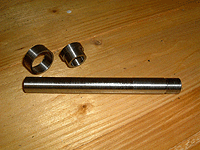 |
The spindle shaft is made from 3 different parts which are glued together. The outer ring is a very light press onto the
inner ring, the inner ring is a tighter press on the spindle. |
Assembly
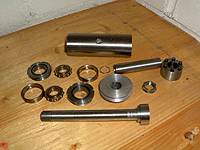 |
31-Dec-06: All parts are now made, there's an extra small ring in there to lengthen the spacer as the
spring box bottoms out before the spacer tightens. The pulley does not have a keyway as
Delta 88 high strength retainer will be
used to affix it to the shaft - once built up, the spindle assembly will not be coming apart. |
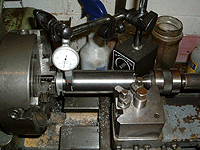 |
01-Jan-07: Holding the spindle by the retaining nut, it's being "clocked" into place. |
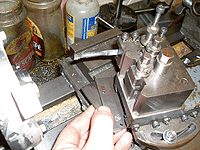 |
The toplide is being set over at 20 degrees and I've made a small gauge up to ensure that the
angle is repeateable every time I need to make anything for this spindle. |
|