Home
Up
|
Over two years, not much has
happened with the Mini Mill CNC Conversion. The original plan of using some cheap
unipolar driver boards, and some 60oz/in steppers has been completely replaced. The motors
now will be 116oz/in (still probably half the size needed) and for now some
Xylotex bipolar chopper drives.
The current spec is for X/Y/Z/A axis control, although the
very poor Z axis on
the mini-mill will be completely replaced. A ballscrew of exactly the right size
was sourced from ebay at the right price making this task a little easier.
Currently, the controllers have been powered up on the bench and
the motors tested. This has been driven by the Artsoft Mach2 software and seems to all
work OK. The controllers are in the process of being installed in a proper case, so
this is about as much as I have pictures for right now...
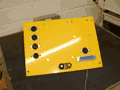 |
26-May-2004: The controller is being built
into an 8"x6" chassis, all components and connectors are attached to the lid of the
case. Down the left side, X/Y/Z/A outputs are 4 pin DIN connectors.
The remaining connectors are terminal posts for main power, 25 way D type that
comes with the Xylotex board, and finally a 5 pin DIN connector for 'power steal' from
the PC.
|
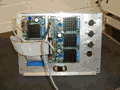 |
Turned the other way up, the two Xylotex boards are visible
along with the connectors for attaching the motors. Now all I have to do
is wire the thing up and test it again.
|
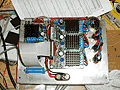 |
28-May-2004 A longer job than expected, but it's all wired
up now. Testing should be complete 29th May, then it's the patterns for all the
castings :-)
|
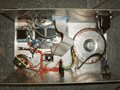 |
24-Aug-2004 Testing failed. Steps were being lost,
this problem was traced to the length of leads between the power supply and the controller.
A new controller on the left was made with a built in power supply - this has eliminated ground
loops and other problems, so far all tests have passed with no missed steps.
|
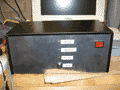 |
Another view of the box, not really much on the front
panel apart from a few LEDs and a fuse.
|
|