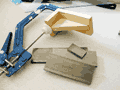 |
11-May-2003: Clamping some wood together to make the pattern for the bracket, also the
steel items have been chopped from stock for the other bits and pieces. Thank goodness for bandsaws...
|
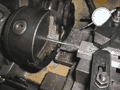 |
17-May-2003: The fixed part of the dovetail has been cut, now in
the lathe so that the nut can be tapped (by hand!) parallel to the face and sides.
|
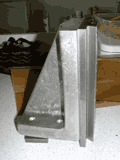 |
18-May-2003: The casting for the bracket has been finished, and the dovetail and backplate
attached. The whole lot is held together with 8 countersunk M3 screws and epoxy adhesive.
|
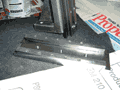 |
23-May-2003: Everything had been going good up until the slide...
The gauge plate strips had been drilled slightly off angle, but the sides of the slides have been ground to mask this.
A total of 12 M3 screws hold the strips to the slide, I managed to drill one side M2.5 to tap M3, and the other side M3 so
no threads - the far side is just held on with glue and the screws used as pins. Not sure if this will hold up or I have
to make another one.
|
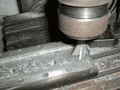 |
9-Jun-2003: No work for a little while due to
other commitments, but back on the vertical slide now and cutting the dovetail.
This is not much fun on the oil hardening gauge plate, cutting off 0.005" each pass.
|
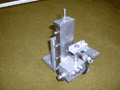 |
11-Jun-2003: Slides now done and lapped in, the dial needs to be made for the top
along with a ball handle to turn the thing. It should now be possible to use the assemblies made so far to graduate
the dial and carry out some primitive gear cutting. More later...
|
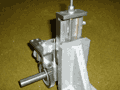 |
View from the back, the gib strip is made from brass - cutting up more gauge plate doesn't appeal
to me right now. If it wears unevenly and/or quickly, it will get replaced. There is also a small brass collar
underneath the top bracket which has been simply tapped M6 to fit the M6 x 1.00 feedscrew and glued to the feedscrew with
epoxy.
|
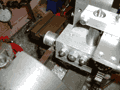 |
12-Jun-2003: There is enough of the machine built to allow it to graduate
its own dial. Fitted with a 50 tooth change wheel, it's an easy task to put 50 graduations on the dial
each representing 0.02mm.
|
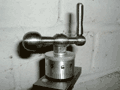 |
Here's the dial along with a very rough ball handle.
The dial graduations were filled in with a Sharpie and came out much better than I had hoped,
although the numbers have been filled in by hand :-(
The ball handle was made with a file and silicon carbide paper - what a mess...
|
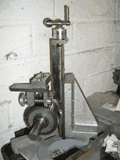 |
That's it for the vertical slide. It certainly works OK but needs a few tweaks
such as a fixed line on the top bracket for reading off the numbers. Time to start work on the pattern
for the base...
|